PROVECTA Process Automation offers two 3-day courses in advanced power plant process dynamics and control loop tuning, which can be delivered on your premises or at a conference venue.
The courses are based on practical knowledge and the application of control theory to power plant processes, aiming to develop a deeper understanding of process dynamics and skills in problem solving and application of test procedures. The format is a combination of interactive presentation, discussion and simulation exercises. Detailed course notes are provided, and extensive use is of made of Simulink® models and tuning calculators which have been developed by PROVECTA for the course. Class size is typically 6 to 12 students.
Simulink® models of boiler and turbine plant components are central to the hands-on tuning exercises that enable each student to see the effects of process characteristics including noise, actuator hysteresis, slew rate limiting, non-linearities, transmitter faults, and interactions with other loops. Plant faults are applied to the models for investigation to develop control system problem-solving skills. Difficult dynamics such as valve non-linearities, inverse drum level response and high-order superheater temperature response are studied, modeled and tuned. MATLAB® and Simulink® are products of The Mathworks.
Module 1
The first module reviews common process responses, controller structures and adjustments including the use of filters, gap action and non-linear gain. Several tuning and calculation methods are compared for relative merits on the power plant environment.
Free tuning calculation software developed by PROVECTA® is provided with the course and several commercial analysis and tuning tools are demonstrated.
The course provides a full set of principles and procedures for testing and adjustment of controller structures including PI, PID, lead-lag PI, Smith Predictor, derivative-model, cascade, multiple drives, adaptive gains and feedforward, with labs using power plant models and realistic controllers.
Module 2
This builds upon Module 1, covering:
- operating characteristics of major plant components such as fans, mills and superheaters to develop a deep understanding of the processes;
- functions, features and performance requirements of major power plant control loops, including different approaches taken in control concepts;
- general structure and tuning of coordinated control systems including Boiler Follow, Turbine Follow and MW control modes;
- performance optimisation and minimisation of control loop interactions;
- functions and limitations of load-frequency control.
For Module 2, dynamic models of the air/gas system, drum/feedwater system, and steam pressure/temperature/flow system enable controllers to be tuned at various loads and tested with load changes and disturbances. Both once-through and drum boiler plant and dynamics can be covered.
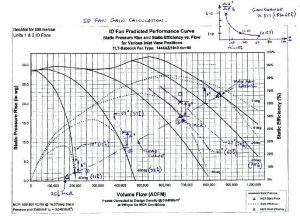
Calculating ID Fan Gain
Should you wish to discuss any aspect of this training course, please contact our modulating contols expert, Mr Don Parker at the following contact details:
Mr Don Parker MEng RPEQ Don.Parker@provecta.com P +1 (224) 420 7982 M +1 (224) 714 7952 |